Industrial seals are essential components used in various industrial applications to prevent leakage, contamination, and damage by providing a secure and reliable barrier between mechanical components, machinery, or systems. These seals come in different forms, materials, and configurations to accommodate diverse operating conditions, pressures, temperatures, and media encountered in industrial environments. Industrial seals play a critical role in ensuring operational efficiency, safety, and environmental compliance across a wide range of industries, including manufacturing, oil and gas, automotive, aerospace, marine, chemical processing, and power generation.
Here’s a comprehensive description of industrial seals:
- Functionality: Industrial seals serve several critical functions within industrial systems and equipment, including:
- Fluid Sealing: Industrial seals prevent the leakage of fluids, such as liquids, gases, or powders, between interconnected components or systems, ensuring containment, safety, and regulatory compliance.
- Environmental Protection: Seals prevent the ingress of contaminants, moisture, dust, or debris into sensitive equipment or processes, preserving product quality, reliability, and longevity.
- Pressure Retention: Seals maintain the integrity of pressurized systems or vessels by containing internal pressure and preventing blowouts, leaks, or catastrophic failures.
- Friction Reduction: Seals reduce friction and wear between moving parts, such as shafts, bearings, or pistons, by providing lubrication and reducing surface contact, extending component life and efficiency.
- Noise and Vibration Damping: Seals dampen noise and vibration generated by rotating equipment, reciprocating machinery, or hydraulic systems, enhancing workplace safety, comfort, and productivity.
- Types of Industrial Seals:
- O-Rings: O-rings are circular seals with a cross-sectional shape resembling the letter “O,” commonly made of elastomeric materials such as nitrile rubber, silicone, or fluorocarbon. They are widely used in hydraulic systems, pneumatic systems, pumps, valves, and fluid connectors to provide reliable sealing against fluid pressure and temperature variations.
- Gaskets: Gaskets are flat or profiled seals placed between mating surfaces to prevent fluid leakage and maintain pressure integrity in static or low-pressure applications. They are available in various materials, including rubber, cork, graphite, and metal, and are used in flanged connections, pipe joints, heat exchangers, and machinery enclosures.
- Mechanical Seals: Mechanical seals are dynamic seals used to prevent leakage between rotating or reciprocating shafts and housing components in pumps, compressors, mixers, and agitators. They consist of stationary and rotating seal faces pressed together by a spring or other mechanism, creating a tight seal against fluid leakage.
- Rotary Seals: Rotary seals, also known as oil seals or shaft seals, are used to prevent lubricant leakage and contamination in rotary applications, such as motors, gearboxes, and wheel hubs. They are typically made of elastomeric materials with a metal casing and lip design to provide effective sealing against oil or grease migration.
- Hydraulic Seals: Hydraulic seals are used in hydraulic cylinders, actuators, and fluid power systems to prevent fluid leakage and maintain pressure integrity under high-pressure conditions. They include piston seals, rod seals, wipers, and wear rings, designed to withstand dynamic motion, high pressure, and temperature fluctuations.
- Pneumatic Seals: Pneumatic seals are used in pneumatic cylinders, valves, and air-powered equipment to prevent air leakage and maintain pressure integrity in compressed air systems. They include piston seals, rod seals, and static seals, designed for low-friction operation and compatibility with pneumatic media.
- Lip Seals: Lip seals, also known as radial shaft seals or oil seals, are used to prevent lubricant leakage and contamination in rotary shaft applications. They feature a flexible lip or sealing element that contacts the shaft surface, creating a barrier against oil or grease migration.
- Custom Seals: Custom seals are designed and manufactured to meet specific application requirements, including unique geometries, sizes, materials, or performance specifications. They are engineered for specialized applications in industries such as aerospace, automotive, semiconductor manufacturing, and pharmaceutical processing.
- Material Composition: Industrial seals are made from a wide range of materials selected based on application requirements, including:
- Elastomers: Rubber compounds such as nitrile, silicone, fluorocarbon, EPDM, or polyurethane are commonly used for their flexibility, resilience, and chemical resistance.
- Plastics: Polytetrafluoroethylene (PTFE), polyethylene (PE), polypropylene (PP), or polyvinyl chloride (PVC) offer excellent chemical resistance, low friction, and temperature stability.
- Metals: Stainless steel, aluminum, brass, or copper alloys provide strength, durability, and corrosion resistance for metal-to-metal sealing applications.
- Composites: Reinforced materials such as fiberglass, carbon fiber, or aramid fibers combined with resins offer high strength, stiffness, and temperature resistance for demanding industrial environments.
- Operating Conditions: Industrial seals are designed to operate effectively under a wide range of conditions, including:
- Temperature: Seals must withstand extremes of temperature, from cryogenic temperatures to high-temperature applications, without compromising sealing performance or material integrity.
- Pressure: Seals are rated for specific pressure ranges, from vacuum applications to high-pressure hydraulic or pneumatic systems, ensuring containment and pressure integrity.
- Media Compatibility: Seals are selected based on their compatibility with the fluids, gases, or chemicals encountered in the application, preventing material degradation or failure.
- Speed and Motion: Seals must accommodate dynamic motion, rotary or reciprocating speeds, and surface contact pressures without excessive wear, friction, or leakage.
- Installation and Maintenance: Proper installation and maintenance practices are essential to ensure the optimal performance and longevity of industrial seals:
- Installation: Seals should be installed according to manufacturer specifications, using proper tools, lubricants, and techniques to achieve correct fit, alignment, and compression.
- Inspection: Regular inspection of seals for signs of wear, damage, or deterioration is necessary to identify and address potential issues before they lead to leakage or failure.
- Replacement: Seals should be replaced at recommended intervals or when performance issues are detected to prevent downtime, equipment damage, or safety hazards.
- Standards and Certification: Industrial seals may comply with industry standards and certifications established by organizations such as ASTM International, ISO (International Organization for Standardization), ANSI (American National Standards Institute), DIN (Deutsches Institut für Normung), or API (American Petroleum Institute). Compliance with standards ensures that seals meet specified performance criteria for quality, safety, and reliability.
- Applications: Industrial gaskets find widespread applications across various industries and sectors, including:
- Oil and Gas: Seals are used in drilling equipment, pipelines, valves, and pumps for sealing against hydrocarbons, corrosive fluids, and high-pressure environments.
- Automotive: Seals are employed in engines, transmissions, brakes, and suspension systems to prevent fluid leakage, contamination, and friction.
- Aerospace: Seals are critical components in aircraft engines, hydraulic systems, landing gear, and fuel systems, ensuring safety, reliability, and performance.
- Chemical Processing: Seals are used in reactors, vessels, pumps, and valves for sealing against corrosive chemicals, high temperatures, and pressure fluctuations.
- Pharmaceutical: Seals are employed in manufacturing equipment

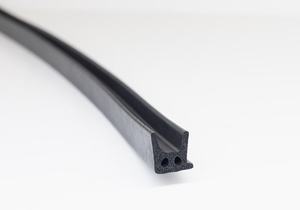

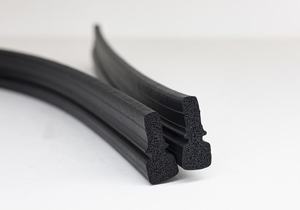




